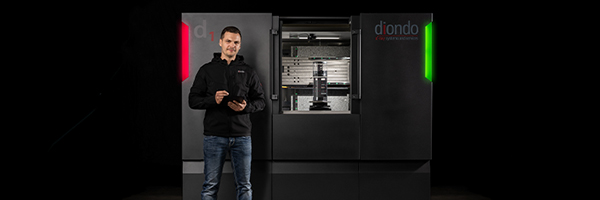
The best of both worlds
New and booming industries, not least the field of e-mobility, place high demands on inspection systems in research, development and quality control. In response diondo has released the new d1 model.
The subject of electromobility is frequently in the news at present. Not least due to the fundamental decisions being made by politicians in the context of making transport more climate-friendly. However, the still comparatively young technology is facing major challenges. The previously profitable internal combustion engine model is to be replaced by the electric motor in rapid steps over the next few years. For manufacturers, this means massive changes in all areas of research and development and production. So far, the field of e-mobility is missing many years of experience that have been acquired over more than a century with the internal combustion engine. Moreover, not only electric motors themselves have to be developed, but also all the systems that are required for production. Many components of an electric motor are highly challenging to manufacture due to their design and the processed materials. This applies especially to the area of quality control, which is becoming increasingly important for manufacturers due to the dangers associated with defects in electric motors and accumulators.
The use of CT systems in industrial quality control has proven its reliability over the past decades. Non-destructive material testing as an accompanying process significantly improves the error rate and reduces costs at the same time. With more than a quarter of a century of experience in the development and manufacturing of industrial computed tomography systems, diondo GmbH is currently one of the leading manufacturers and service providers. With a new model in the successful series, the compact but at the same time powerful and high-resolution diondo d1, the company from Hattingen in North Rhine-Westphalia is addressing the current requirements of the industry.
"More and more frequently, our customers are faced with the challenge of having to inspect components made of challenging and high-density materials," explains Kai Völkel, Head of Inspection Services & Applications at diondo GmbH. " This involves increasingly complex components, such as battery cells for electromobility, which have to be analysed with high resolution despite their size and density."
Classic CT systems work with reflection tubes as the radiation source. The high power required to penetrate challenging materials or thicker walls of components negatively affects the maximum resolution. In simple terms, the higher the used power, the lower the resolution. Longer measurement times are required to compensate for this phenomenon. On one hand this often leads to inadequate inspection results, and on the other hand, extended measurement times result in long-term economic disadvantages.
With the new model d1, diondo closes the gap between small ultra-high-resolution systems such as the diondo dsubµ and high-performance models suitable for larger demanding components such as the diondo d2.
"By using a high-power transmission X-ray source, we can achieve a four times higher resolution with the diondo d1 compared to conventional systems for the same measurement duration or alternatively, with the same resolution, we can shorten the measurement duration by a factor of four," emphasizes Mr. Völkel. "We thus offer our customers a true all-rounder that is equally suitable for challenging tasks and the efficient inspection of high quantities in the shortest possible time, e.g. in additive manufacturing or industrial injection moulding production."
The compact system operates with only one tube, which is offered in different performance classes as required. Compared to common double-tube systems, diondo d1 is thus not only more powerful than the competition, but also affordable and low maintenance.